Achieving Unparalleled Stamping Consistency in High-Volume Production
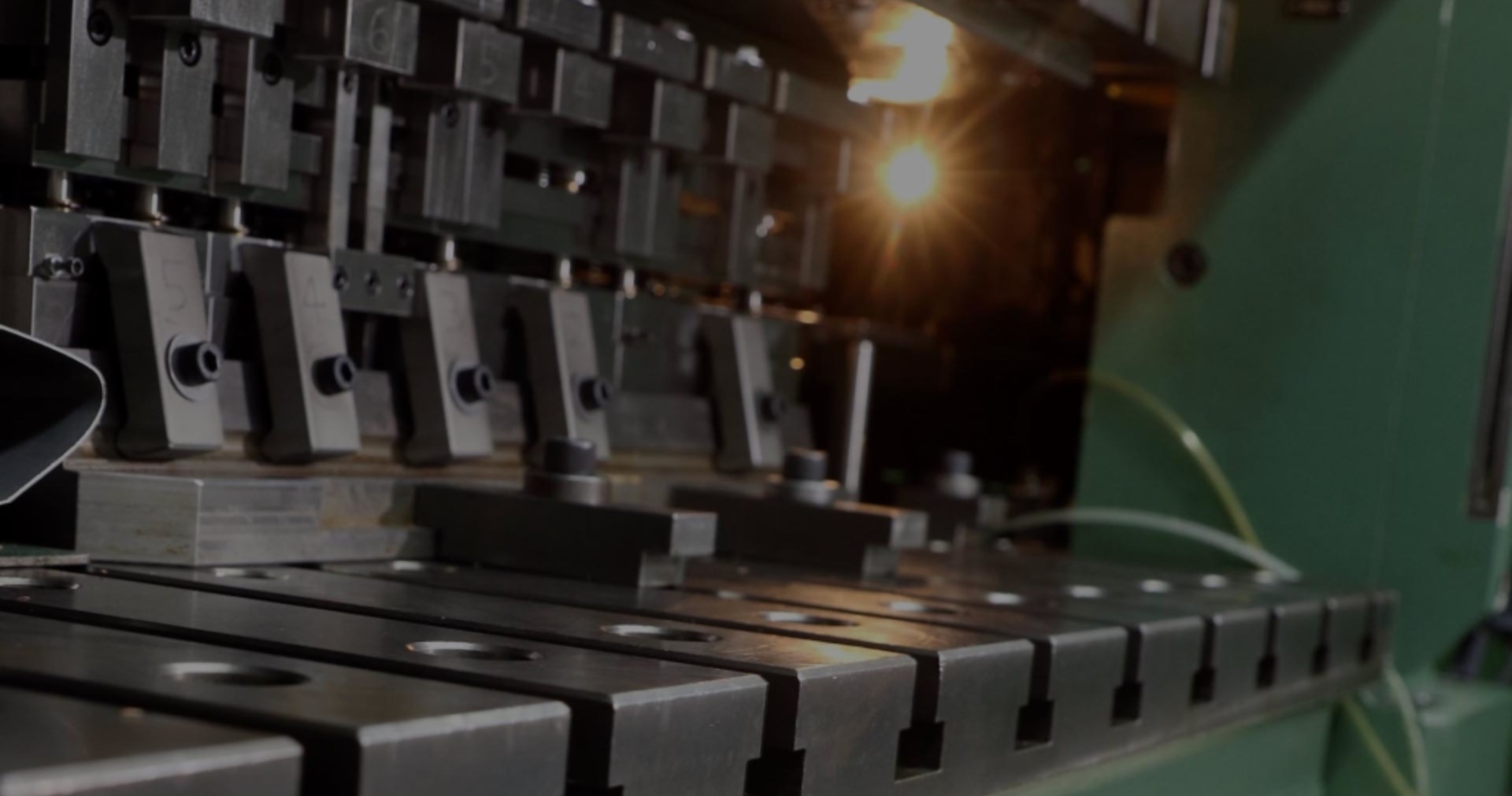
In high-volume metal stamping, consistency is crucial
This precision process - vital in manufacturing various components - demands strict accuracy and repeatability. This consistency ensures each part meets high quality standards, crucial for reliability and performance in end products.
In large-scale production, small deviations can lead to big issues, making unparalleled consistency essential for maintaining product integrity and minimising waste.
Batten & Allen exemplifies excellence in precision metal stamping. With extensive experience and a commitment to quality, they are industry leaders, especially in high-volume scenarios.
Catering to diverse industries, Batten & Allen's expertise ensures every component they manufacture embodies precision and reliability – all while leveraging advanced technology and stringent quality control to consistently produce superior stamped components.
Table of Contents
- 1. The Importance of Consistency in Metal Stamping
- 2. Batten & Allen’s Approach to Precision Stamping
- 3. Advanced Technology in Stamping
- 4. Quality Control Measures for Consistency
- 5. Material Selection and Handling
- 6. Skilled Workforce and Training
- 7. Meeting Industry-Specific Needs
- 8. The Future of High-Volume Metal Stamping
1. The Importance of Consistency in Metal Stamping
The critical role of consistency in metal stamping, particularly in high-volume production, can’t be understated. In industries where precision is paramount - such as automotive, electronics, and aerospace - the slightest variation in metal stamping can lead to significant discrepancies in the final product.
Consistency ensures that each component not only fits perfectly, but also performs its function flawlessly, contributing to the overall integrity and safety of the product.
In high-volume production, the demand for uniformity is even more pressing. Here, the replication of components in large quantities must adhere to exact specifications, with minimal tolerance for error.
This level of consistency is crucial for maintaining quality control, reducing waste, and optimising efficiency. Ultimately, this separates a successful production run from one plagued with costly recalls and repairs.
For manufacturers, achieving this consistency is a testament to their craftsmanship and attention to detail, directly impacting their reputation and customer trust.
From the perspective of the end user, consistency in metal stamping translates to reliability and satisfaction. Products that incorporate consistently stamped components are more likely to perform as expected, have a longer lifespan, and require less maintenance. This reliability enhances the user's experience, fostering trust in the brand and loyalty to the product.
In sectors like medical devices or automotive safety components - where the stakes are incredibly high - the importance of consistent quality is even more pronounced.
As a whole, consistency in metal stamping is a critical factor that influences not just the manufacturing process but the entire lifecycle of a product. It affects everything from production efficiency and cost-effectiveness to customer satisfaction and brand reputation.
In a market where excellence is expected and competition is fierce, the ability to produce consistently high-quality stamped components is a definitive edge for any manufacturer.
2. Batten & Allen’s Approach to Precision Stamping
The precision stamping methods used at Batten & Allen confirm our commitment to excellence and consistency in the field of high-volume production.
Our process is a blend of advanced technology, skilled craftsmanship, and rigorous quality control, ensuring that each component produced meets the highest standards of precision and reliability.
At the core of Batten & Allen's precision stamping process is the use of state-of-the-art machinery and technology. This includes advanced stamping presses capable of handling a wide range of materials with extreme accuracy. Our ability to work with a diverse range of materials and thicknesses is crucial in catering to the varied needs of different industries.
To ensure consistency, we employ a range of customised solutions. Understanding the unique requirements of each project, we tailor our stamping solutions to ensure not only the functionality but also the cost-effectiveness of each component. This collaborative approach is key to success in delivering products that precisely meet customer specifications.
Quality assurance is another critical aspect of the precision stamping process. Batten & Allen has rigorous quality control measures in place to ensure that every stamped component is compliant with the highest industry standards. This commitment to quality is evident in our meticulous design process and expertise in both stamping and plating, offering unparalleled precision and cost-effectiveness.
Leveraging cutting-edge technology and continual investment in technological advancements, Batten & Allen optimises the stamping process to achieve superior precision. This commitment to staying at the forefront of the sector underscores our dedication to delivering high-quality components efficiently and reliably.
3. Advanced Technology in Stamping
In the precision metal stamping industry, the deployment of advanced machinery and technology is pivotal for achieving high levels of accuracy and consistency. This section delves into the sophisticated equipment and techniques that are commonly used in precision stamping and explores how automation and precision engineering contribute to maintaining consistent quality in high-volume production.
Advanced Machinery and Technology
Stamping relies on state-of-the-art presses, capable of handling a diverse range of materials with exceptional precision. These presses are designed to operate with high accuracy, essential for producing components that adhere to stringent specifications. The ability to work with various materials, from ultra-thin strips to thicker sheets, is crucial for catering to the diverse needs of different sectors, including automotive, electronics, and aerospace.
Role of Automation
Automation is a key factor in enhancing efficiency and ensuring consistency in the stamping process. By automating repetitive and precise tasks, manufacturers significantly reduce the risk of human error, leading to a higher degree of uniformity in each batch of components produced. Automated systems maintain consistent operational parameters, such as speed and pressure, essential for achieving uniformity in the final products.
Precision Engineering
Precision engineering is integral to the stamping process, especially when dealing with intricate designs or materials requiring tight tolerances. Precision-engineered machinery ensures that each stamping action is executed with meticulous accuracy, a necessity for components that must fit and function flawlessly within complex assemblies.
The integration of advanced technology, automation, and precision engineering in the metal stamping industry is essential for meeting the high-quality standards demanded in today's market. This technological sophistication enables manufacturers to produce components with a level of precision and consistency that is vital for the success of a wide range of products and applications.
4. Quality Control Measures for Consistency
Achieving consistency in precision metal stamping hinges significantly on quality control measures. Regular inspections and comprehensive testing are vital in this process, ensuring that each component not only meets but maintains high standards throughout production.
These measures are the backbone of a consistent output, crucial for industries where precision is non-negotiable.
Regular inspections play a key role in achieving consistency.
They involve scrutinising components at various stages of the stamping process, allowing for immediate correction of any deviations. This proactive approach is essential in maintaining uniformity across batches.
Inspections can vary from simple visual checks to more intricate assessments involving dimensional accuracy and material properties. They ensure that every component adheres to the predetermined specifications, thereby maintaining a consistent quality standard.
Testing complements inspections by rigorously evaluating the components against set performance criteria.
This includes assessing the durability, strength, and functionality of the stamped products under different conditions. Such testing is especially critical in sectors like automotive and aerospace, where component reliability is directly linked to safety. By subjecting products to these tests, manufacturers can assure that their components consistently perform as intended, even under strenuous conditions.
The overarching goal of these quality control measures is to uphold a uniform standard of excellence.
Regular inspections and testing enable manufacturers to detect and address potential issues before they escalate, ensuring that each product batch remains consistent with the last. This not only bolsters product reliability but also enhances the manufacturer's reputation for delivering consistent quality.
5. Material Selection and Handling
The selection and handling of materials is fundamental to achieving consistent stamping results. The quality of the material directly influences the integrity and performance of the stamped components, making it a critical factor in the production process.
Material quality plays a pivotal role in ensuring that each stamped component maintains uniformity in dimensions, strength, and durability.
High-quality materials reduce the likelihood of defects such as cracks, warping, or inconsistencies in thickness, which can compromise the stamping process and the final product. For instance, materials with consistent grain structure and composition provide a stable base for stamping, leading to more predictable and uniform outcomes. This is particularly important in high-volume production, where consistency across large batches is essential.
The handling of materials is equally important in maintaining consistency.
Proper storage and handling procedures ensure that the materials retain their quality until they are used in the stamping process. Factors such as humidity, temperature, and exposure to contaminants can affect the material properties, leading to variability in the stamping results. Therefore, controlled storage conditions and careful handling are critical in preserving the material quality.
Furthermore, the compatibility of the selected material with the stamping process and the intended application of the component is a key consideration.
Different materials behave differently under the stresses of stamping, and choosing the right material for the specific application ensures that the components perform consistently in their end-use environment. This involves understanding material properties, such as ductility, hardness and tensile strength, and how they interact with the stamping process.
The use of high-quality materials, combined with proper handling practices, ensures that stamped components are consistently produced to the highest standards.
6. Skilled Workforce and Training
The success of the precision metal stamping process is heavily reliant on the skills and expertise of the workforce.
Skilled labour is a critical component in achieving high-quality, consistent results in stamping operations. The intricate nature of metal stamping requires a deep understanding of machinery, materials, and the nuances of the stamping process, making the role of a skilled workforce indispensable.
Skilled workers bring a level of craftsmanship and attention to detail that is essential for precision stamping. They possess the ability to operate complex machinery with precision, monitor the stamping process for quality, and make adjustments as needed to maintain consistency. Their expertise is particularly crucial when dealing with complex designs or materials that require special handling. Skilled workers can identify potential issues before they become problematic, ensuring that the production process runs smoothly and efficiently.
Training is another key aspect of maintaining a skilled workforce in the metal stamping industry. Continuous training programs are essential to keep the workforce up-to-date with the latest technologies and techniques in metal stamping. This includes training on new machinery, updates in stamping techniques, and quality control measures. A well-trained workforce is more adept at handling the challenges that come with precision stamping, leading to better quality control and consistency in the final products.
Moreover, the skilled workforce plays a vital role in innovation and improvement within the stamping process. Their hands-on experience and knowledge can lead to process optimisations, contributing to the overall efficiency and effectiveness of stamping operations.
In summary, a skilled workforce is fundamental to the success of precision metal stamping.
Their expertise, combined with ongoing training, ensures that the stamping process is carried out with the highest level of precision and consistency. This not only enhances the quality of the stamped components but also contributes to the overall productivity and competitiveness of the stamping industry.
7. Meeting Industry-Specific Needs
In the diverse landscape of precision metal stamping, meeting the specific needs of different industries is a complex yet crucial aspect. Companies like Batten & Allen exemplify how processes can be tailored to cater to the unique requirements of sectors such as automotive and electronics, each with its distinct challenges and standards.
Tailoring Processes for Different Industries
In the automotive industry, for example, components must fit precisely - but also withstand extreme conditions. Batten & Allen addresses these needs by employing robust materials and precision engineering techniques that ensure the durability and reliability of automotive components like sensors and connectors. The precision stamping process is fine-tuned to handle the stress and wear that automotive parts are subjected to, ensuring longevity and performance.
The electronics industry, on the other hand, requires components that are not only precise but also miniature in size. Batten & Allen adapts its stamping processes to produce small, intricate parts with high precision. This involves using advanced technology capable of handling delicate materials and executing precise stamping operations, essential for components like semiconductor parts and connectors.
Challenges and Solutions in Maintaining Consistency
Maintaining consistency across these varied applications presents its own set of challenges. Each industry has different tolerances, material requirements, and performance expectations. To address these, Batten & Allen implements a versatile approach, adapting their machinery and processes to suit the specific material and design requirements of each industry.
Quality control measures are tailored to the specific standards of each sector. For automotive components, this might involve rigorous stress testing, while for electronics, precision measurements and electrical testing are more pertinent. By customising their quality control processes, Batten & Allen ensures that the components meet the exact standards of each industry.
Ultimately, meeting industry-specific needs in precision metal stamping requires a combination of specialist processes, adaptable technology, and stringent quality control measures. Companies like Batten & Allen demonstrate how these challenges can be met effectively, ensuring consistency and quality across various applications, from the robust needs of the automotive industry to the intricate demands of electronics manufacturing.
8. The Future of High-Volume Metal Stamping
As we look towards the future of high-volume metal stamping, the industry is poised for significant advancements and emerging trends that promise to enhance consistency and efficiency. These developments are not just technological but also encompass shifts in industry practices and approaches to meet evolving demands.
Emerging Trends and Advancements
One of the key emerging trends in metal stamping is the increasing integration of automation and robotics. This shift promises to bring even greater consistency and precision to the stamping process, as automated systems can maintain exacting standards with minimal variation. Additionally, advancements in materials science are leading to the development of new alloys and composites that offer improved strength, flexibility, and durability, expanding the possibilities for stamping applications.
Another significant trend is the adoption of Industry 4.0 technologies. This includes the use of IoT (Internet of Things) devices, AI (Artificial Intelligence), and machine learning algorithms to enhance process control and predictive maintenance. These technologies enable real-time monitoring and adjustments, ensuring consistent quality and reducing downtime.
Companies like Batten & Allen are actively adapting to these changes, positioning themselves to meet future challenges and capitalise on new opportunities with a continued focus on consistency, quality and customer satisfaction.
As we look towards the future of metal stamping, it’s clear that companies like Batten & Allen are well-equipped to navigate the evolving landscape of manufacturing.
Our dedication to maintaining high standards of quality and consistency, while embracing technological advancements, sets a benchmark in the industry.
Explore the world of precision metal stamping with Batten & Allen: Mastering Metal Stamping
Getting Started with Batten & Allen
Whether you're looking for a long-term partnership or need assistance with a specific project, Batten & Allen's approachable and professional team is ready to guide you through the process.
Contact us now!