Decoding Stamping Reliability Metrics:
What They Mean for Your Products
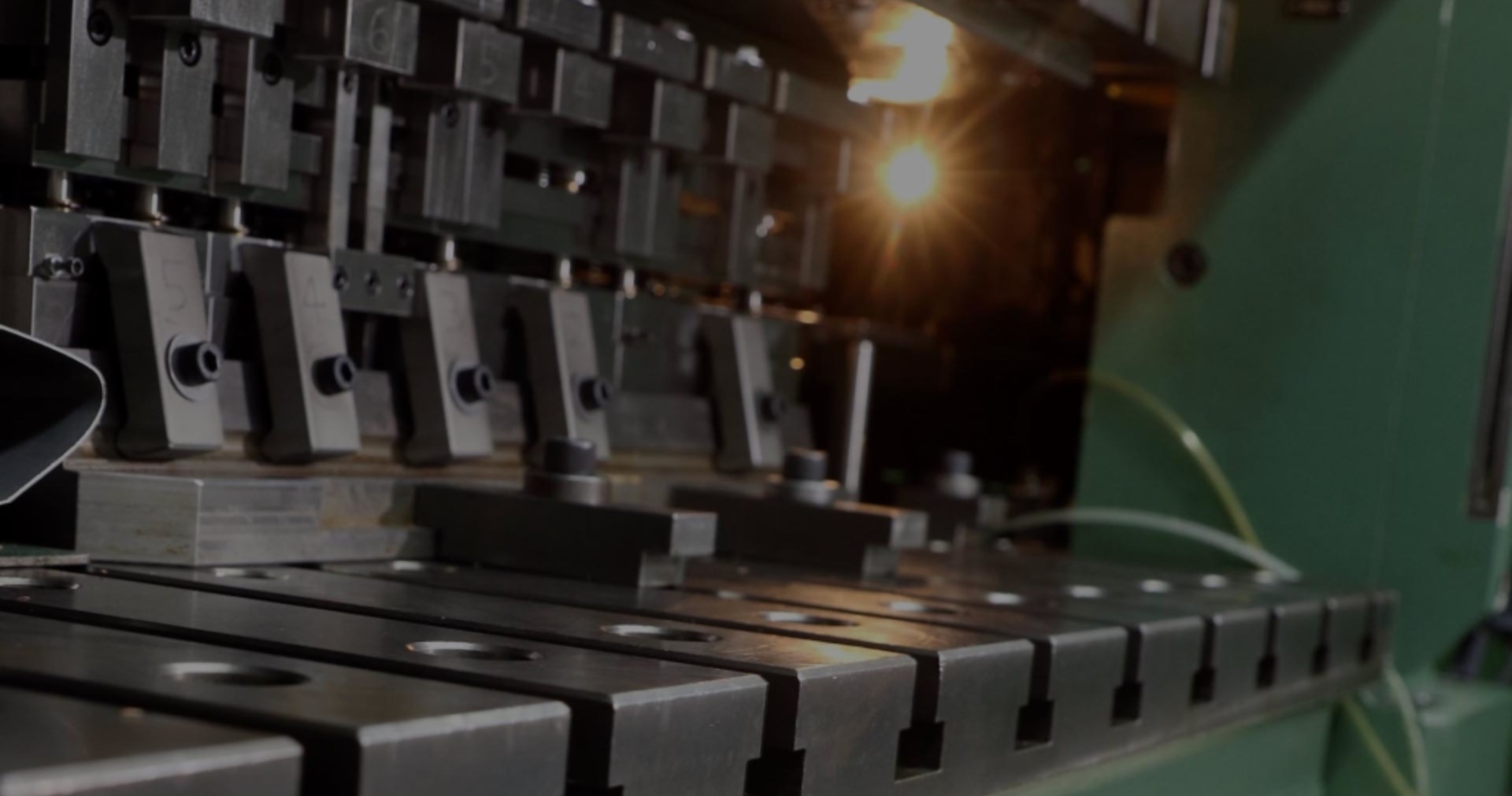
In the precision-driven world of metal stamping, reliability metrics serve as the cornerstone for assessing and ensuring product quality
These metrics - encompassing aspects like dimensional accuracy, material strength, and surface finish - are indicators of a product's conformance to design specifications, as well as predictors of its performance and longevity.
The importance of these metrics becomes particularly evident when considering the end-use of stamped components, which often find critical applications in industries such as automotive, electronics, and aerospace. In these sectors, even minor deviations can lead to significant functional discrepancies, affecting the overall performance and safety of the final product.
The impact of reliability metrics extends beyond the manufacturing floor, directly influencing customer satisfaction and brand reputation.
Consistently meeting these metrics translates to products that perform as expected, are durable, and require less maintenance over their lifespan. This reliability fosters trust in the product, and - by extension - the brand, leading to higher customer satisfaction.
In contrast, failure to adhere to these metrics can result in product recalls, customer dissatisfaction, and damage to the brand's reputation. Therefore, in the competitive landscape of manufacturing - where quality and reliability are paramount - these metrics are not only measures of compliance, but are integral to maintaining a company's market position and customer trust.
Table of Contents
- 1. Understanding Stamping Reliability Metrics
- 2. Dimensional Accuracy and Tolerances
- 3. Material Strength and Durability
- 4. Surface Finish and Quality
- 5. The Role of Advanced Technology in Enhancing Reliability
- 6. Quality Control and Assurance in Stamping
- 7. Industry-Specific Reliability Requirements
- 8. The Impact of Reliability Metrics on End-User Satisfaction
- Unlock the Power of Precision Stamping with Batten & Allen
1. Understanding Stamping Reliability Metrics
Serving as key indicators of the quality and performance of stamped products, reliability metrics are a crucial component of the metal stamping industry.
Stamping reliability metrics are quantifiable standards that assess various aspects of a stamped component's quality - from its physical dimensions, to its material properties and surface characteristics. These metrics are essential for ensuring that each stamped product not only meets design specifications but also performs reliably in its intended application.
Common metrics used in the industry include:
- Dimensional accuracy. This refers to the degree in which the stamped part matches its specified dimensions - a critical factor in applications where precise fit and function are necessary.
- Material strength metrics. Tensile strength and yield strength, for example, evaluate the durability and load-bearing capacity of the material used. This ensures that the final product can withstand operational stresses.
- Surface finish metrics. These assess the quality of a part's surface, including its texture, smoothness, and any defects. This is particularly important for components that require a high-quality aesthetic finish, or where surface characteristics impact functionality, such as in electrical conductivity.
Together, these metrics provide a comprehensive overview of a stamped product's reliability and suitability for specific applications. Adhering to these metrics is vital for manufacturers to produce high-quality, reliable components that meet the demands of various industries, from automotive to electronics.
2. Dimensional Accuracy and Tolerances
Dimensional accuracy in metal stamping refers to the degree in which stamped parts conform to the specified dimensions in their design.
This accuracy is crucial to ensure each component fits precisely in its final assembly.
In industries where components must interact seamlessly - such as in automotive or aerospace engineering - the importance of dimensional accuracy cannot be overstated. Maintaining tight tolerances (the allowable limits of variation in a part's dimensions) is essential to ensure the functionality and integrity of the final product.
Tight tolerances are particularly important in high-precision applications. They ensure that parts fit together correctly without requiring additional modifications, which can increase production time and costs.
In assemblies where multiple parts must function in unison, even minor deviations in size can lead to malfunctions, reduced efficiency, or even complete system failures. For instance, in an automotive engine, parts with improper dimensions could lead to increased wear and tear, resulting in a shorter lifespan and potential safety hazards.
Furthermore, dimensional inaccuracies can have far-reaching consequences beyond immediate functional issues. They can lead to increased scrap rates, higher rework costs, and delays in production schedules. Moreover, consistently producing parts that fail to meet dimensional specifications can damage a manufacturer's reputation for quality and reliability. Therefore, maintaining dimensional accuracy and tight tolerances is not just a matter of meeting technical specifications but is also integral to maintaining market competitiveness and customer trust.
3. Material Strength and Durability
In the world of metal stamping, material strength and durability are critical factors that significantly influence the lifespan and reliability of the final product. Material strength metrics, such as tensile strength and yield strength, are key indicators used to assess a material's ability to withstand operational stresses without failure.
Tensile strength measures the maximum stress a material can withstand while being stretched or pulled before breaking, whereas yield strength refers to the maximum stress that a material can endure without permanent deformation. These metrics are crucial in selecting materials for specific applications, ensuring that the stamped parts can sustain the mechanical loads and environmental conditions they will encounter in use.
The durability of the material directly impacts the product's lifespan. Durable materials that maintain their integrity over time under various conditions are essential for products that require long-term reliability, such as automotive components or structural elements in construction. The choice of material not only affects the product's ability to perform its intended function but also influences maintenance needs and the likelihood of replacement over time.
There is a strong correlation between material choice and product reliability. Selecting the right material with appropriate strength and durability characteristics is vital for ensuring that the stamped products can reliably perform as expected. This decision is based on a thorough understanding of the operational environment, the stresses the product will face, and the desired longevity. By carefully considering these factors, manufacturers can ensure that their products not only meet the immediate functional requirements but also offer sustained performance and reliability over time.
4. Surface Finish and Quality
The surface finish of stamped products plays a crucial role in both their functionality and aesthetic appeal.
In precision metal stamping, the surface finish refers to the texture, smoothness, and overall quality of the exterior of a stamped part. This aspect is particularly important because it can significantly impact the product's performance, especially in applications where surface properties are critical.
Common surface finish metrics include roughness - which measures the texture of a surface at a microscopic level - and glossiness, which indicates the surface's shine and reflectivity.
These metrics are essential in industries where the surface finish can affect the product's performance. For instance, in electrical components, a smoother surface can enhance conductivity, while in consumer products, a high gloss finish might be desirable for aesthetic reasons.
The implications of surface finish extend beyond mere appearance. In many cases, the surface quality can influence the product's durability and resistance to environmental factors like corrosion or wear. A well-finished surface can provide an additional layer of protection against such external elements, thereby extending the product's lifespan.
Likewise, surface quality is often a reflection of the overall integrity of the product. A high-quality surface finish can enhance the perceived value of the product, contributing to customer satisfaction and brand reputation.
In competitive markets, the attention to detail in surface finishing can be a differentiating factor, showcasing the manufacturer's commitment to excellence.
5. The Role of Advanced Technology in Enhancing Reliability
Progressive technology plays a pivotal role in enhancing the reliability of metal stamping processes.
Precision engineering and automation are at the forefront of these technological advancements, significantly improving reliability metrics in stamping outcomes. Precision engineering involves the use of high-precision tools and equipment that can produce components with extremely tight tolerances; this level of precision ensures that each part is consistent with its design specifications, thereby enhancing the overall reliability of stamped products.
Automation, on the other hand, brings consistency and efficiency to the stamping process.
Automated stamping presses and handling systems can operate with a high degree of accuracy and repeatability, reducing the likelihood of human error and ensuring uniform quality across large production volumes. Automation also allows for continuous operation, which can increase production rates while maintaining consistent quality.
An example of technology improving stamping outcomes can be seen in the use of computer-aided design (CAD) and computer-aided manufacturing (CAM) systems. These technologies allow for precise design and planning of the stamping process, enabling manufacturers to simulate and optimise the process before actual production. This pre-planning can identify potential issues and allow for adjustments, ensuring a smoother and more reliable production process.
Another case involves the integration of real-time monitoring systems in stamping equipment. These systems can track various parameters such as force, pressure, and temperature during the stamping process. By monitoring these parameters, manufacturers can quickly identify and correct any deviations from the standard process, ensuring consistent quality and reducing the risk of defects.
The integration of advanced technology in metal stamping, including precision engineering and automation, significantly enhances the reliability of the stamping process. These technologies ensure that stamped products are produced with high precision and consistency, meeting the stringent quality standards required in various industries.
6. Quality Control and Assurance in Stamping
In the metal stamping process, quality control and assurance play a vital role in ensuring the reliability and consistency of stamped products.
Quality control processes, such as regular inspections and rigorous testing, are implemented at various stages of production to detect and address any deviations from the set standards.
These inspections can range from visual checks to more detailed examinations using precision measuring instruments, ensuring that each component adheres to its specified dimensions, material properties, and surface finishes.
Testing is another integral part of quality control in stamping. It involves subjecting the stamped components to various conditions and loads they are expected to encounter in their actual use. This could include stress tests, durability tests, and functionality tests, which help in verifying that the products can withstand operational demands and maintain their integrity over time.
Quality assurance, on the other hand, encompasses a broader scope, focusing on maintaining consistent reliability metrics throughout the production process. It involves establishing and adhering to a set of procedures and standards that guide the stamping process, from the selection of raw materials to the final output. Quality assurance ensures that every step of the process is optimised to produce components that consistently meet the required quality standards.
The role of quality assurance isn’t just to maintain the quality of individual components - It’s also key to ensuring the overall reliability of the production process. This includes continuous monitoring and analysis of production data, identifying trends or potential areas of improvement, and implementing corrective actions when necessary.
By maintaining stringent quality control and assurance practices, manufacturers can ensure that their stamped products are reliable, consistent, and meet the high standards expected by their clients and the end-users.
7. Industry-Specific Reliability Requirements
Different industries have unique reliability needs and standards, which significantly influence the metal stamping process.
In the automotive industry, for instance, reliability is centred around safety and durability. Automotive components must withstand extreme conditions like vibrations, temperature fluctuations, and long-term wear and tear.
Metrics such as fatigue resistance and impact strength are crucial in this sector. Automotive standards, like the ISO/TS 16949, dictate stringent quality requirements to ensure the safety and longevity of automotive parts.
In the electronics industry, the focus is on precision and miniaturisation.
Components like circuit boards and connectors require exact dimensional accuracy and fine surface finishes to ensure proper functionality. Reliability metrics in electronics often include electrical conductivity and thermal resistance, governed by standards like IPC-A-610 for electronic assemblies, ensuring that components perform reliably in various electronic applications.
The aerospace industry demands the highest levels of reliability due to the critical nature of its applications. Aerospace components must endure extreme environmental conditions, including high altitudes, varying pressures, and temperature extremes.
Metrics such as tensile strength, corrosion resistance, and fatigue life are paramount. Aerospace standards, like the AS9100, encompass comprehensive quality management systems for the design and manufacture of aerospace components, ensuring they meet the rigorous safety and performance requirements.
Each of these industries requires specific approaches to metal stamping to meet their unique reliability standards. Manufacturers must adapt their processes, from material selection to quality control measures, to ensure that their products meet the specific needs and standards of these diverse sectors. This adaptability is key to achieving the high levels of reliability demanded in automotive, electronics, and aerospace applications – as well as many more.
8. The Impact of Reliability Metrics on End-User Satisfaction
The link between stamping reliability and customer satisfaction is both direct and profound.
When stamped components consistently meet reliability metrics, they invariably contribute to the overall quality and performance of the end product. This reliability resonates with end-users, who often equate the dependability of the product with fulfilment of their needs.
For instance, in the automotive industry, the reliability of stamped parts like brake components directly impacts the safety and performance of the vehicle - a critical factor in customer assurance.
Moreover, the long-term benefits of high reliability extend far beyond immediate customer satisfaction. Consistently reliable products help in building a strong brand reputation; in markets where competition is fierce, a reputation for quality and reliability can be a significant differentiator.
This reputation, built over time through consistent product performance, fosters customer loyalty. Loyal customers are not only likely to return for repeat purchases but are also more inclined to recommend the brand to others, effectively becoming advocates.
Furthermore, high reliability in stamped products can lead to reduced warranty claims and fewer recalls, which are both costly and damaging to a brand's reputation. By investing in reliability metrics, manufacturers can avoid these pitfalls, ensuring a positive and lasting impression on their customer base.
Overall, the commitment to stamping reliability is an investment in customer satisfaction and long-term brand credence – which are essential components for sustained success in any industry.
Stamping reliability metrics are critical to various industries, highlighting how dimensional accuracy, material strength, surface quality, and the integration of advanced technology contribute to the overall reliability of stamped products.
These metrics are pivotal in meeting industry-specific requirements and ensuring end-user satisfaction, directly impacting brand reputation and customer loyalty.
The consistent adherence to these reliability metrics not only ensures the production of high-quality components but also fosters trust and confidence among customers, which is essential for the long-term success and growth of a business.
In the competitive landscape of manufacturing, where quality and precision are paramount, the focus on stamping reliability metrics emerges as a key differentiator - driving product excellence and business prosperity.
Explore the world of precision metal stamping with Batten & Allen: Mastering Metal Stamping
Getting Started with Batten & Allen
Whether you're looking for a long-term partnership or need assistance with a specific project, Batten & Allen's approachable and professional team is ready to guide you through the process.
Contact us now!